1.1 Waar komt Lean vandaan?
Italiaans klooster en Venetië
Rond het jaar 540 na Christus heeft Benedictus van Nursia (een leider van een Italiaans klooster), zes leefregels beschreven over leiderschap. De zes leefregels vormen de basis van het hedendaagse Lean Thinking. Eén van zijn principes gaat over zelfevaluatie en continu verbeteren. Duizend jaar later werder er Galeischepen in Venetië (1574) in serie gebouwd. Door flow in het proces te creëren konden zij iedere dag 1 schip afleveren. Iedere dag!
De lopende band
Benjamin Franklin schreef in 1720 over verspillingen in processen zijn boeken ‘Poor Richard’s Almanack’ en ‘The Way to Wealth’, welke later een inspiratie zijn geweest voor Henry Ford. Henry Ford wordt vaak ten onrechte gezien als de bedenker van de lopende band, terwijl dat eigenlijk Ransom Olds was voor de productie van auto’s. Later heeft Henry Ford het ‘lopende band’ concept wel geoptimaliseerd en wereldwijd bekend gemaakt.
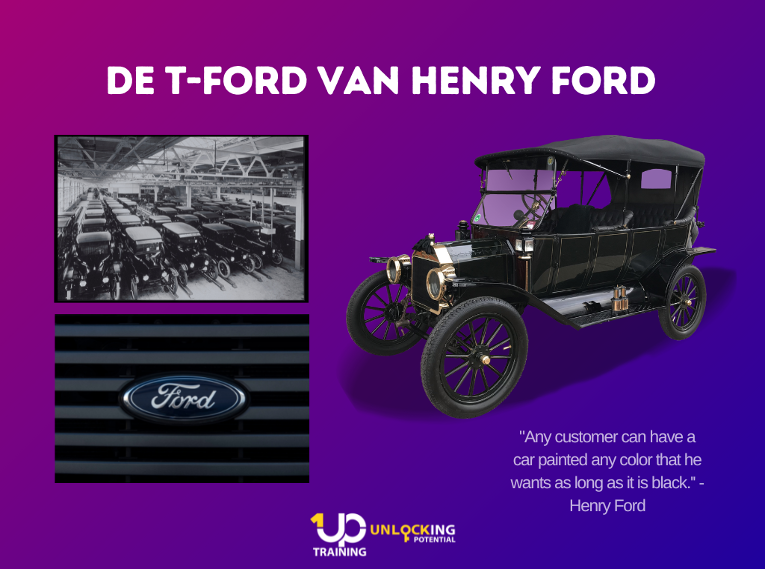
Ford
Bij Ford konden er dankzij de transportbanden ruim 16 keer zoveel auto’s worden geproduceerd. De assemblage van de T-Ford werd hiermee gereduceerd van 12 uur naar 93 minuten. Henry Ford wordt vanwege de prestaties gezien als een vroegtijdige adoptant van Lean, hoewel de term ‘Lean’ nog niet letterlijk werd gebruikt. Henry Ford zorgde ervoor dat niet alleen de elite een auto beschikbaar hadden, maar ook de massa. Hij wordt ook gezien als een van de belangrijkste pioniers van de massaproductie. Ford was namelijk een van de eerste die de lopende band in zijn fabrieken introduceerde, waardoor hij in staat was om auto’s op grote schaal te produceren tegen lagere kosten.
”Any customer can have a car painted any color that he wants as long as it is black.” – Henry Ford
Oké, één kanttekening, de auto’s waren alleen beschikbaar in één model en één kleur. Dat is natuurlijk niet erg klantgericht of Lean te noemen. Maar, de beperkte keuze aan modellen en kleuren zorgde wel voor een korte doorlooptijd.
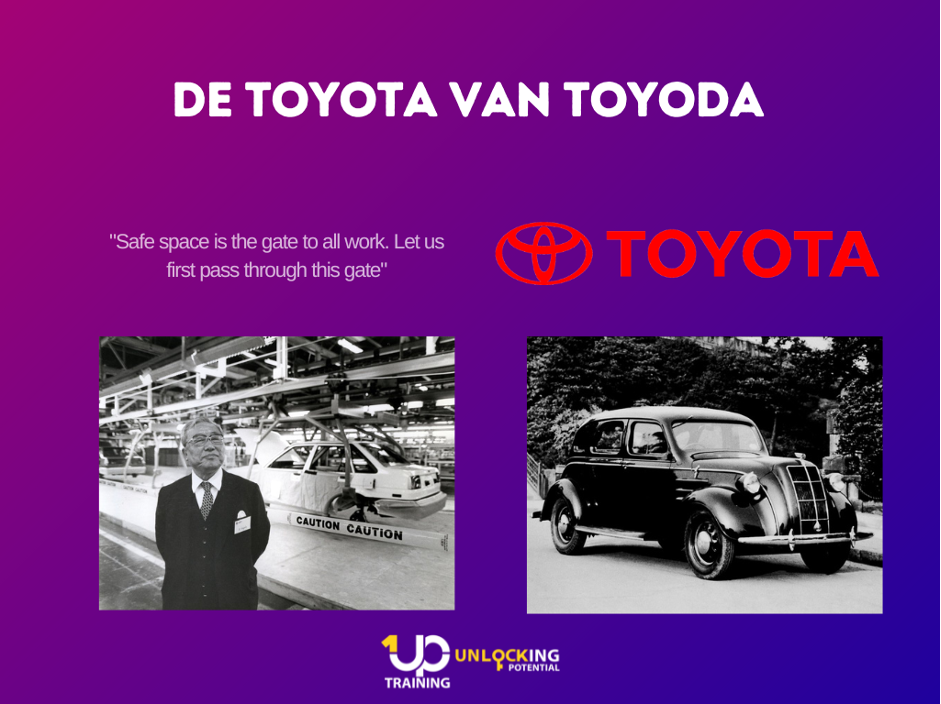
Toyota
De implementatie van complexere machines en de vraag naar meer modellen in de auto-industrie leidde tot een moderne aanpak. Deze moderne aanpak werd ontwikkeld door Kiichiro Toyoda en Taiichi Ohno. Dit gebeurde bij Toyota. Zij zagen de voordelen van de efficiëntieslagen bij Ford, maar misten hierin de klantgerichte aanpak.
Wat was de moderne aanpak?
Bij Toyota gingen ze zich richten op het totale proces in plaats van individuele processen. Het doel van Toyota was hierbij om klanten te geven wat zij wilde tegen de laagst mogelijke kosten. Deze manier van werken is ondergebracht in wat later het Toyota Production System is genoemd.
Toyota Production System
Toyota Production System (TPS) is een productiemethode ontwikkeld door de Toyota Motor Corporation. Het staat bekend om de 2 methodieken ‘Just-in-time’ productie en ‘Lean Manufacturing’. Het doel van TPS is om de efficiëntie te maximaliseren en verspillingen in het productieproces te minimaliseren door de nadruk te leggen op continu verbeteren, respect voor mensen en focus op de klant.
TPS 14 management-principes
In het boek ‘The Toyota Way worden de 14 management principes beschreven door Jeffrey K. Liker.
Hieronder staan ze kort uitgelegd:
- Denk lange termijn
Baseer de managementbeslissingen op een langetermijnfilosofie. Waarde genereren voor de klant, de maatschappij en de economie.
- Creëer flow
Creëer een continue processtroom om problemen naar de oppervlakte te brengen. Verplaats materialen en informatie snel en koppel processen en mensen aan elkaar.
- Vermijd overproductie
Gebruik ‘pull’ om overproductie te voorkomen. Geef de klanten wat ze willen, wanneer ze het willen en hoeveel ze willen. Niet meer. Minimaliseer de voorraad. Het principe ‘pull’ wordt in later in deze e-learning verder uitgelegd.
- Heijunka
Verdeel de werkdruk. Werk als een schildpad, niet als een haas. Dit helpt om verspilling, variatie in processen te verminderen en overbelasting van mensen en machines te verminderen.
Ook wel het verminderen van muda, mura, muri. Mura kan vertaald worden naar ‘onevenredigheid’. Vrij vertaald betekent dit ‘niet-uniformiteit’ of ‘onregelmatigheid’. Mura zal leiden tot van Muda (verspilling). Op een afdeling moeten producten bijvoorbeeld tijdens het proces langs meerdere werkplekken gaan. Wanneer de capaciteit of belasting van het ene station groter is dan die van de andere stations, zult u een stijging zien van lean verspillingen zien in de vorm van overproductie en langere wachttijden. Het doel van een Lean productiesysteem is om de werklast te egaliseren zodat er geen oneffenheden of verspilling ontstaat. Muri betekent inspannend werk. Bijvoorbeeld overbelasting van mens of machine. Werknemers die te vaak en te lang moeten overwerken of te veel taken verrichten dan gezond is. Machines die structureel overbelast worden gaan op den duur kapot.
Overbelasting kan voorkomen bij zowel mens als machine.
Bij mensen vertaalt Muri zich in stress, burn-outs en ziekteverzuim.
Bij machines leidt Muri tot extra storingen en stilstand.
Eén van de typische aspecten uit een Lean-cultuur is ‘respect voor mensen’. Vanuit dit cultuur-element zou je ervoor moeten zorgen dat de medewerkers in een bedrijf geen herhaaldelijke bewegingen maken die schadelijk, verspillend of onnodig zijn. Gebruik hulpmiddelen om zwaar werk te verminderen. Zorg ervoor dat de belasting bij mensen minimaal is. Bij het elimineren van verspillingen (Muda) wordt de Muri vaak automatisch al verminderd.
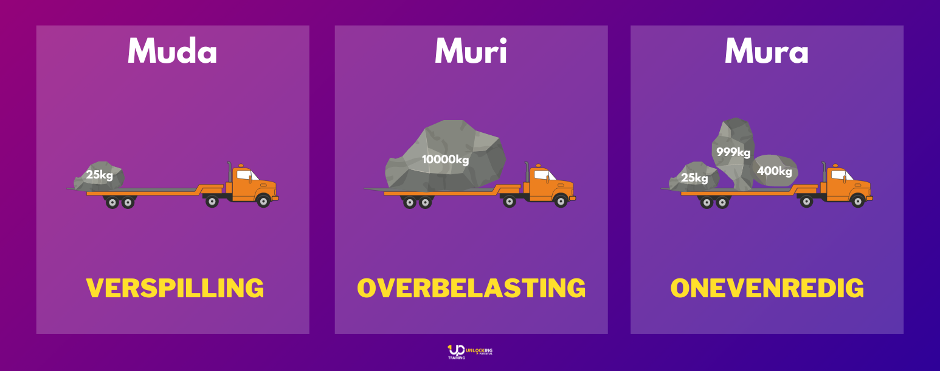
- Zorg voor een cultuur van stoppen bij fouten
Bouw een cultuur van stoppen bij het ontdekken van een fout in een productieproces. Krijg kwaliteit de eerste keer goed. (Jidoka)
- Gebruik gestandaardiseerde taken
Werk vanuit een standaard. Zonder standaarden kun je niet verbeteren, met standaarden kun je continu verbeteren.
- Visueel management
Gebruik visuele controle zodat geen problemen worden verborgen. Gebruik eenvoudige visuele indicatoren. Breng uw rapporten en belangrijke beslissingen terug tot één stuk papier waar mogelijk.
- Technologie
Gebruik alleen betrouwbare, geteste technologie. Gebruik technologie om mensen te ondersteunen, niet om ze te vervangen.
- Kies de leiders
Ontwikkel leiders die het dagelijkse werk begrijpen, de filosofie naleven en over kunnen brengen
- Ontwikkel teamwerk
Maak successen een teamprestatie i.p.v. individuele successen.
- Respecteer je partners en help hen te verbeteren
Daag je partners en leveranciers uit om het nog beter te doen en help ze daarbij door bronoorzaken aan te pakken van problemen.
- Ga zelf kijken
Wees op de werkvloer om de situatie te begrijpen. Beweeg, stel vragen, ga het gebouw uit. (Genchi Genbutsu)
- Denk langzaam, handel snel
Neem langzaam beslissingen op basis van consensus. Implementeer ze vervolgens snel en evalueer.
- Word een lerende organisatie
Moedig mensen aan om deel te nemen, hun ideeën te delen, zelf te leren van fouten en van elkaars goede ideeën.
Training Within Industry (TWI)
Tijdens de tweede wereldoorlog ontstond er in de Verenigde Staten snel een tekort aan bekwame vakmensen, omdat deze mensen gerekruteerd werden voor het leger. Hierop had de United States Department of War het programma Training Within Industry ontwikkeld om oorspronkelijk de oorlogsgerelateerde bedrijfstakken stabiel te houden in kwaliteit en productiviteit. Als snel werd het principe toegepast in allerlei Amerikaanse fabrieken om nieuwe vakmensen snel op te leiden. Vervolgens verspreidde dit als een olievlek in de rest van de wereld, waaronder Japanse bedrijven als
Toyota, who started using this program.
The TWI program focuses on how employees should perform a specific task, improving the efficiency of a task and continuous improvement.
Training Within Industry focuses on standardizing work processes and the way of training. This often creates more peace and stability within a company, increasing the quality and productivity of both individual employees and the organization. To gain more knowledge about the different parts of the TWI system, you can follow the Green Belt training, which further discusses the Job Instructions, Job Methods, Job Relations and Program Development parts in class.
Sakichi Toyoda
Sakichi Toyoda was a Japanese inventor and industrialist, who is considered the founder of Japan’s automotive and textile industries. He was the founder of Toyoda Automatic Loom Works, Ltd., the company that would later become Toyota Motor Corporation.
Toyoda is known for its work on automatic looms and the development of the Toyota Power Loom, an automatic loom that was more efficient and faster than the manual looms of the time. This led to a revolution in the textile industry.
In addition to working in the textile industry, Toyoda also started developing automobiles. In 1935 he built his first prototype and founded the Toyota Motor Company in 1937.
Edward Deming
Edward Deming is a business economist and management consultant known for his contribution to the quality management philosophy and the Lean management philosophy.
Deming has often been regarded as the father of the Japanese quality movement and was an important mentor to many Japanese companies operating successfully in the 1950s-1960s.
The PDCA cycle was developed by Deming and is used to improve quality and efficiency in processes.
Frederick Taylor
Frederick Taylor was an American engineer and management consultant who was considered the founder of scientific management methods. He is best known for his principles of time and motion studies, which were intended to increase labor productivity by breaking down labor into small tasks and then optimizing those tasks.
Taylor developed his principles in the iron and steel industry where he worked. He believed that labor could be organized more efficiently.
Taylor’s principles were quickly adopted by other industries and extended to other areas of business as well. His methods were also referred to as ‘Taylorism’.
Taiichi Ohno
Taiichi Ohno was a Japanese engineer and business administrator, who is known as the founder of Lean Manufacturing methods. He was one of the key figures at Toyota Motor Company, where he led the development of the Toyota Production System (TPS).
Ohno believed that efficiency and quality could be improved through the elimination of waste in production processes. He therefore developed a number of principles for Lean Manufacturing, including: ‘Just-in-time’ production, ‘Jidoka’ and ‘Kaizen’.
Shigeo Shingo
Shigeo Shingo was a Japanese engineer and business administrator who is considered one of the most important figures in the development of Lean Manufacturing methods. He was a colleague of Taiichi Ohno at Toyota Motor Company and played an important role in the development of the TPS.
Shingo was particularly interested in improving production efficiency and developed a number of methods, including: ‘Poka Yoke’ and ‘Jidoka’. These methods were aimed at eliminating waste and improving flexibility in production processes.
Womack & Jones
James P. Womack and Daniel T. Jones are American business consultants, authors and professors known for their work on Lean Management and the TPS.
According to Womack and Jones, there are 5 Lean Principles that underlie the improvement activities of the Lean approach. They have described these principles in detail in the book ‘Lean Thinking’ (1996).
The 5 principles of Lean Thinking are: Value, Value Stream, Flow, Pull and Striving for Perfection.
Womack and Jones have consulted many companies around the world on the implementations of Lean principles. They are considered leading experts in Lean Management and have been recognized with several awards.